The advantages of off-site construction
The future of construction will be off-site and wood will be an important part of that change
The introduction of environmental concerns is redirecting the concept of quality in construction to aspects more related to environmental value, through what is known as eco-efficient construction.
The growing demand for large-sized timber for large-scale projects arises from this new paradigm and imposes a different operationalisation of the construction process which highlights the management of time and process in the planning phase, in detriment of the actual construction phase. This reorganisation is changing the supply chain as a whole and requires appropriate resource management to enable sustaining productivity and profits.
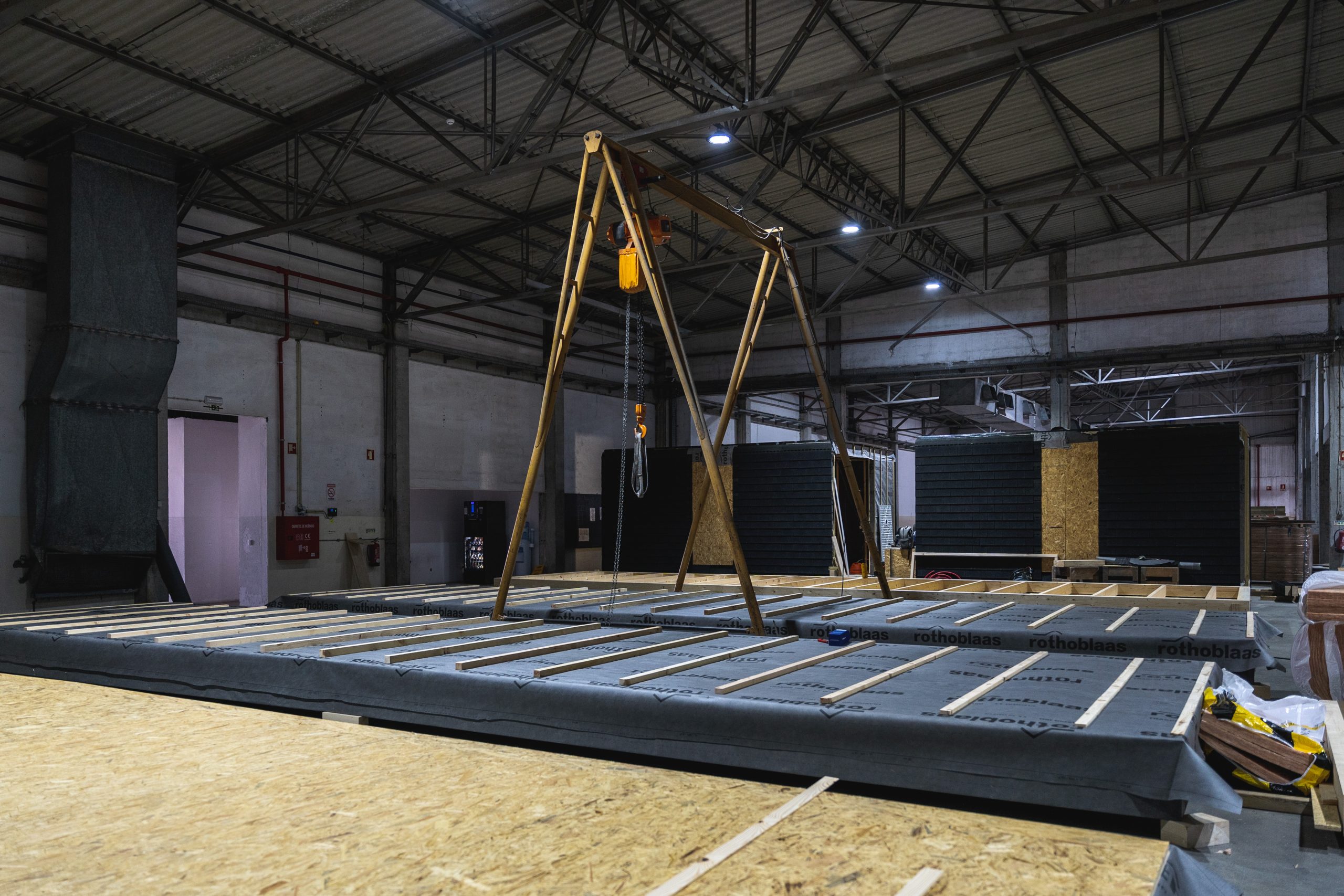
Prefabrication of off-site construction are among the best solutions to achieve efficient management, not only because this consolidates a major part of the value chain and automatically compels the parties involved to engage in planning.
The concept of prefabrication is hardly recent. It received a booster shot as a result of a new environmental awareness, arising from the growing urbanism, directed towards the production of constructions adapted to the environment and the requirements of their users. The development of digital imaging tools has expanded the range of possibilities, giving rise to the innovation in the sector.
There has been some resistance to the introduction of new systems and technologies in the construction sector, not due to technical issues of implementation, but above all as a result of cultural habits in this traditional sector which is characterised by a low technological level.
This resistance of one of the sectors with strongest economic impact at a national level is the main limitation to the adoption of new construction processes. However, action is becoming increasingly urgent so that this sector too can become a strong driver of the development and growth of eco-efficient construction.
Being a sector resilient to change, construction sector is essentially based on the abundant use of worksite labour, in which the employment of the available technologies is sometimes untapped, with a very slow evolution in the structure and mode of operation of the sector’s companies (Smith 2009).
Smith. 2009. History of Prefabrication: A Cultural Survey.
Off-site construction is radically changing the rules of architectural design
The popularity of pre-designed and pre-fabricated houses is growing, boosted by contemporary surging values such as the environmental conservation and energy efficiency they foster.
Countries such as Singapore, Australia and the United Kingdom have adopted modular construction to meet the shortage of labour and housing, and Sweden already uses this form of architecture in 90% of single-family residences. Modular construction has been used in various developed countries all worldwide for the construction of buildings, from small houses to multi-storied buildings. This is a construction method with a long-standing presence throughout history which has been surprising in its quality, structural performance and due to offering mobility to the buildings. In Japan, off-site constructions have been remarkable in their application of technology and due to the dimensions of constructed buildings.
In Portugal, this technology has been gradually gaining ground over recent years and could contribute to achieving the environmental goals of the European Union (EU) and reducing construction costs, thus enhancing the sector’s competitiveness and sustainability.
With the appearance of new technologies which enable viewing projects in 3D, prefabrication has received a strong boost and has started to change the construction scenario. Digital imaging tools, among which is the outstanding Building Information Model BIMconstruction technology, enable gathering together all the project’s information and planning all the stages of the enterprise in a precise manner throughout its entire life cycle.
This context of intelligent design and sharing of projects gives rise to the possibility of multidisciplinary work which can evolve from the phase of review of their technical and economic feasibility to their planning, budgeting and construction. This allows architects, builders, engineers and other parties involved to participate in all the project’s phases.
Alongside this,Open Sourceenables users located in any part of the world to download their favourite home design, and e-commerce platforms like Amazon or Alibaba can send prefabricated materials to the construction site.
Technology is necessarily one of the crucial components of this new quest for off-site construction, which is expected to represent an opportunity for architecture, for engineering, but also for the construction industry.
The concept of prefabrication has revolutionised the way of conceiving architecture, opening the door to a vast number of possibilities for the future and the way that we imagine the world. Building outside the implantation site, producing large-sized structures in factories or even entire buildings with a millimetric precision unleashes a world of possibilities in the construction industry.
All the processes of the traditional construction industry, strongly affected by the on-site conditions which could hinder the efficiency and practicability of a construction are easily substituted by efficient automated operations, with high precision and minimum probability of human error.
Being a centralised process, off-site construction guarantees swiftness, quality and durability for the construction work, combined with lower coordination efforts, in addition to embodying one of the most sustainable methods of construction. This centralisation of the off-site process also enables greater predictability of costs and less disturbance of the implementation site, causing a lower environmental impact and assuring greater sustainability.
Buildings produced, constructed in the fastest and most efficient manner can also more easily meet the growing housing needs of an ever-rising global population, which is believed to increase by 2 billion people by 2050 efficiently allocating the available resources. The high-quality and highly efficient houses produced benefit from the opportunities that digitalised and pre-designed construction can offer. The integration of digital imaging technologies, such as BIM, has made it possible to plan and innovate according to needs and requirements, and innovations such as Open Source, enable that creativity to also involve the customers who are not only able to intervene in the personalisation of the design but, likewise, in the full conceptualisation of the project.
This conception of efficient and collaborative design, which is much more flexible as an innovative construction method, has revolutionised the way that we perceive architecture, urban planning and comfort. Intelligent, green and adaptable projects are those that currently represent sustainability as a construction solution.
The growing dynamism and evolution of off-site construction are due to the development and improvement of the construction materials, combined with the use of new technologies endowing them with a higher quality, , versatility and structural performance than traditional construction systems.
Innovative materials which are high-performance, light and also sustainable have begun to emerge with a superior quality, mechanical properties and durability. Various products on the market that meet these requirements have begun to offer comprehensive solutions in a very low execution time. This is the case of eco-friendly materials such as Novelio Nature, a wall coating in fibreglass or Saint-Gobain, resistant laminated plaster boards for walls and ceilings which, when used in a VDM Prefabricated House, can be ordered, personalised online and built in 99 days. This project is a perfect illustration of what prefabrication can offer in a short space of time, using materials which are of a superior quality, adaptable, large-sized, with high structural rigidity, aesthetically pleasing and respect the environment.
International companies such as Intrastack offer another type of solution designed to implement multi-story projects, with fast construction based on recycled materials which are 70% lighter than those available for traditional construction. This panelised, light gauge steel frame solution can provide a comprehensive construction structure, offering greater efficiency and reducing the need for extensive on-site construction works.
The growing popularity of multiple timber panels that are compressed, nailed or glued together, known as mass timber, has triggered the emergence of a whole supplementary industry to structural members, such as prefabricated beams, columns, slabs, walls and panels for façades, and specialised companies, such as International Timber and Scotframe which offer sustainable, customisable prefabricated kits with a superior efficiency and cost-effectiveness.
Not only directed at the residential segment, prefabricated structures are equally valid for public buildings or large-scale commercial spaces. For example, Saint-Gobain contributed to the construction of a prefabricated hospital in Catalonia and the prefabricated ISOVER F4 façades enable the performance of interior and exterior thermal insulation functions at Saint-Joseph hospital, in Paris.
The growing interest in rehabilitation has also fostered a significant increase in the offer of appropriate and efficient solutions for the renovation of existing buildings. For example, Glava Reform, offers a fast renovation system with small prefabricated panels to coat exterior walls, meeting current ventilation and insulation requirements, effectively modernising and updating constructions in need of rehabilitation.
The current concern with environmental conservation embodies a challenge at a global level and contemporary off-site construction has proved to be a competitive and appropriate solution, with creative and innovative features that are rapidly able to adapt to a world undergoing constant change.
By incorporating digital, precise and collaborative technologies with innovative, high-quality, light and high-performance materials, architects currently have an array of flexible tools that are able to provide structurally effective and aesthetically superior solutions for the challenges of access to housing, at very competitive prices suited to different needs. Prefabricated construction changes the risk profiles of the enterprises and their management, enabling construction to become a disciplined project, endowed with technical knowledge and feasibility from the very initial stage of the project. Nowadays, it is possible to present prefabricated structures that are large-sized, with high structural efficiency, versatility and which are economically viable, able to compete with constructions built on-site .. Prefabricated construction has offered diversified and innovative off-site solutions, and its dynamism is a strong indicator of the path that construction will be taking in the future.
Related Articles
UncategorizedConstruction with Wood
Engineered Wood Market Size & Share Analysis
Government has introduced a statutory tree and woodland cover target which commits to increasing…
Why Choose Wood?Construction with Wood
Timber in construction roadmap
Government has introduced a statutory tree and woodland cover target which commits to increasing…
Durability of construction with wood
The durability of a timber construction can be high. There are examples of wooden churches…