Constructing in CLT
Constructing in CLT
Cross Laminated Timber (CLT) is a wood-derived product which emerged in Switzerland, towards the end of the 1980s, having been subsequently developed in Austria, under a research project involving industries and universities aimed at using wood members of smaller dimensions. From then onwards, the product spread throughout Central Europe, Japan, New Zealand, Australia, Canada and the United States for the construction of single-family houses (Figure 1), residential buildings, multi-storey buildings (due to its good seismic performance) (Figure 2), public buildings, industrial and commercial buildings, and even bridges.
The use of this wood derivative has become popular, driven by the current environmental concerns. The good acceptance of CLT construction systems is also explained by the easy connection between components; lower waste of raw material; low waste generation; clean, dry and organised construction; fast assembly; automated and computerised production process; competitive costs in relation to traditional materials; among others.
The first buildings constructed with CLT appeared in Switzerland in 1993, Germany in 1995, and Austria in 1998. From that time onwards, CLT production increased from approximately 0.095 million m³ in 2000 to 0.61 million m³ in 2010 (Dovetail Partners, 2016).
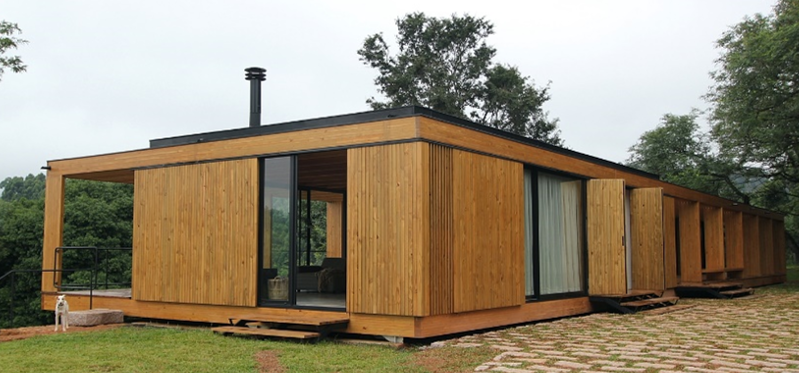
Figure 1: Single-family house in CLT (Crosslam, 2022)
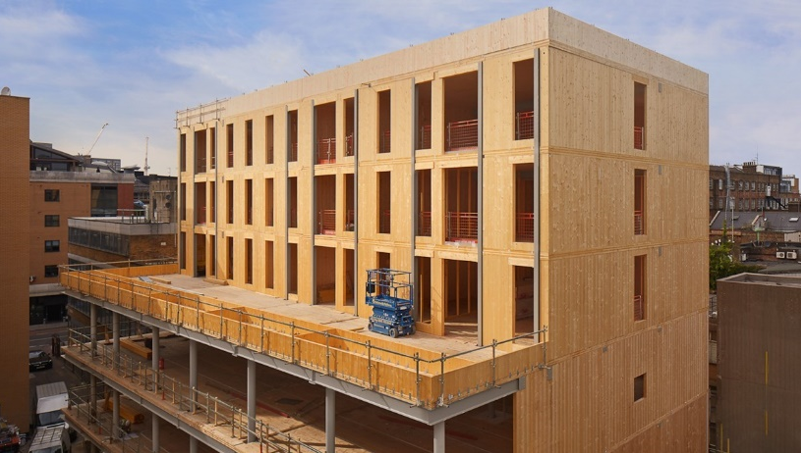
Figure 2: Multi-storey building in CLT (Madeira e Construção, 2022)
CLT is composed of an uneven number of solid structural timber laminates, in order to create an axis of symmetry in the central layer. The European standard (EN 16351, 2014) establishes that the laminates must be 20-40 mm thick and that the width of the parts must be greater or equal to four times their thickness, using laminates of a width of 150 mm as standard. The wood is selected, complying with the technical values required by the quality and control standards; dried in a kiln, stabilising to a water content of 12%, with variations of more or less 2%, so as to ward off attacks by insects and fungi feeding on or living within wood; sawn; glued; and pressed in a crossed manner, using a structural polyurethane reactive (PUR) adhesive free of solvents and formaldehydes.
The crossed configuration of the timber laminates (Figure 3) enables achieving much higher resistance and rigidity capacities, both on and off-plane. CLT is considered a dimensionally stable material, as the crossing of the laminates restricts the wood’s hygroscopic movements when subject to water content variations (less than 1% in the direction of the grain and 2% in the direction perpendicular to the grain). For such, CLT is produced with strict control of the water content of the boards comprising the member, approximately 12%, leaving the factory with a water content between 10 and 14% (Silva et al., 2012).
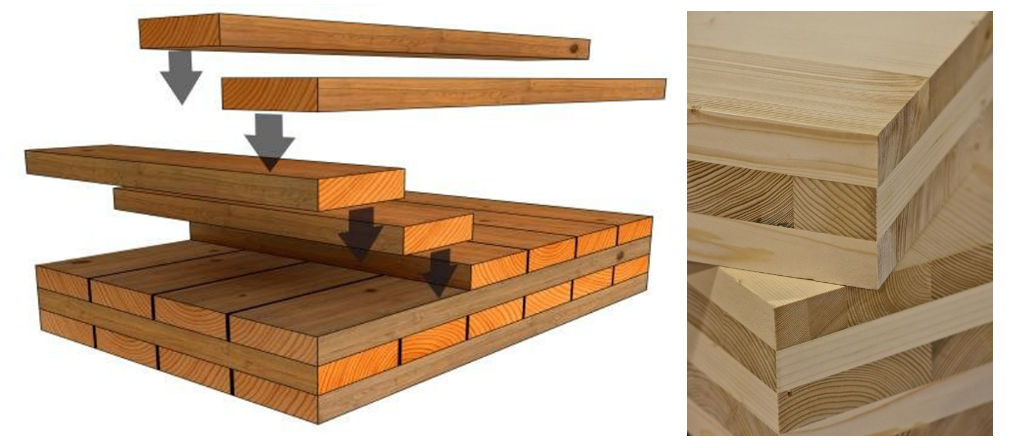
Figure 3: CLT Laminates (CTE, 2022)
Compared to other types of structural systems commonly used in timber construction, this system offers new possibilities in terms of load transfer. In contrast to portico systems in which the loads are predominantly transmitted in unidirectional flows, in CLT panel structures, the members behave like boards, with the load transmission being bidirectional. Thus, one of the key innovations of CLT is based on the production of members in panel form, unlike the usual linear members, which can be used as wall or slab members. The high load-bearing capacity, combined with its low weight, enables extremely slender members, even for spans of large dimension.
CLT panels are prefabricated, arriving on-site already with holes, cuts and openings for fitting parts together, doors, windows and pipelines. The cuts and drilling are made by Computer Numeric Control (CNC), using Computer-Aided Design/Computer-Aided Manufacturing (CAD/CAM) and Building Information Modelling (BIM), ensuring the compatibility of the different project stages. The shape of the cut is specified in the detailed plans/speciality projects, and the cuts are carried out with a high degree of precision. This reduces the waste on-site, which is immediately sent for possible reuse at the factory. Mass production thus enables cost-cutting, as well as stricter quality control of the entire process.
In terms of structural functions, CLT panels can be: panels for ceilings and floors, designed to support the structure’s specific load, where the main direction of the load is perpendicular to the axis of the panel’s intermediary layer; panels for wall structural members (Figure 4a), designed to support the resulting loads, in particular of the building’s height, where the main direction of the load is aligned, in other words, parallel to the axis of the panel’s middle layer; combined structures, based on 3D layout (Figure 4b), for three-dimensional projects forming housing units using CLT panels, which support loads in different directions.
After its production, whether in panels or in 3D modules, they are transported to the construction yard and assembled with simple lifting devices, requiring low use of labour.
With suitable planning, their arrival on-site is coordinated with the assembly team, enabling the immediate assembly of the structure and requiring a minimum construction yard area. The easy, fast and efficient assembly of the structure arises from the large dimensions of the panels, which can reach a length of about 16 m, width of 3 m and thickness of 50 cm. The maximum length of the panels is limited by transport restrictions, while the width is limited by the capacity of the CNC equipment. The assembly of walls and slabs simply by fitting them together reduces the number of possible errors and, as this is done almost entirely “dry”, this enables the almost simultaneous installation of other technical systems and application of interior and external cladding and coatings.
The level of biological durability of the panels naturally depends on the wood species used and its conditions of application and use. According to the European Technical Approval (ETA) documents, the panels’ use is limited to risk classes 1 and 2, corresponding to sheltered exposure without direct contact with weather conditions (NP EN335-1:2011). Under these circumstances, high but not persistent humidification may occur, consistent with typical situations of buildings indoors or roofs outdoors. Added to the natural durability of the species that are normally used (EN 350-2:1994), it is advisable to apply a preserving fungicide and biocide product. The definition of the useful life of the panels is stated in the European Technical Approval documents as 50 years.
The connection of the CLT structure to the foundation, usually in concrete, is extremely important, in view of the wood’s susceptibility to humidity. Accordingly, effective construction techniques should be implemented, in order to prevent an early deterioration of the wood.
The union between the walls and flooring can be materialised in different way, such as fastening with screws and metal connectors made of aluminium, stainless steel or galvanised steel (Figure 5).
The panels’ thermal conductibility properties show unique values among construction materials with structural capacity. The good performance of wood in the cold season comes from the absence of repeating thermal bridges and low number of non-repeating (linear) thermal bridges associated with the construction system. The absence of repeating thermal bridges is explained by the homogeneity of the material between adjacent members and consequent inalterability of the thermal conductibility conditions. These last two points are particularly significant as, due to the current regulatory restrictions, in traditional structures, the problem of repeating and non-repeating thermal bridging imposes extra care, requiring more complex implementation methods, entailing higher costs and greater risks of future complications. In this field, the implementation of CLT structures proves to be a solution that is more simple, more competitive and implies lower thermal losses.
Due to its hygroscopic properties, wood has a similar effect to that of a vapour retardant, being able to absorb, retain and release moisture. The construction thus has some capacity to ensure the natural regulation of the air humidity content, resulting in an excellent indoor environment and healthy conditions inside the houses. In the winter, with low humidity, the wood’s capacity to transport it is low and increases as soon as the wood, indoors, is adjusted to the summer climate.
In acoustic terms, the high density of CLT panels contributes to satisfactory performances. However, for more demanding solutions, the acoustic performance can be improved by introducing absorbent material, for insulation against air traffic sounds, and layers of resilient material at rigid bridges (contact between panels), for insulation against percussion sounds.
As noted above, the CLT prefabrication process enables drilling slots for passing through pipes and cables using CNC equipment (Figure 6). However, their layout requires careful study and analysis taking into account issues of structural nature and background noise levels. In the structural walls, the slots should be drilled in the vertical direction (main structural direction), leaving a minimum safety distance from the lateral top of 10 cm. The slots should be drilled on opposite sides of the same transversal section of the wall, where a minimum distance of 1 m is recommended, thus also ensuring uniformity of the acoustic insulation. Slots on flooring should conceptually follow the same care taken on the walls.
An alternative solution is to fasten the pipes and cables onto the panels, thus reducing the number of cuts and holes. In this case, an interior cavity is created between the CLT surface and plasterboard, for example, which could be filled with insulation material, if it is necessary to increase the construction’s thermal performance. This solution also contributes to the structure’s protection against fire which, once engaged, exempts the need to insert metal connectors inside the CLT. However, this measure precludes exploring the aesthetic value of the CLT panels, which, in indoor environments, may not require cladding or coating for flooring, walls and ceilings (Figure 7).
As to the interior cladding and coating, in addition to plasterboard, the CLT panels can also be painted. In wet areas or more humid environments, conventional coating can be used, such as tiles. However, as a natural construction material, wood performs in harmony with nature throughout its entire useful life. The volume of timber panels swells and shrinks according to ambient humidity, although the timber panel maintains a stable shape due to their transversal pressing and gluing together. It is, therefore, inappropriate to place tiles directly on the panel’s surface, as the bending arising from the tiles, changing the panel’s shape, may lead to undesired deformations.
Different coatings may be combined on the façades, such as cement boards, aluminium, steel, cork and wooden ventilated façades. For such, it is important to ensure ventilation levels of these façades which will increase in proportion to the densities of the cladding and coating materials. Correctly dimensioned anti-vapour barriers should also be applied, in order to protect the timber panels from condensation and potential problems of early deterioration.