Construction Systems
If I want a timber house, which systems are available to me?
Log house
A log house (Figure 1) consists of stacked wooden logs, which can be solid structural timber or glue laminated timber, according to the geometry of the log and, of course, the supplier, normally with a flat internal side and a bevelled external side. The wood parts are stacked through a longitudinal fitting system, forming structural walls that cross at angles with half-lap joints to consolidate and secure the construction.
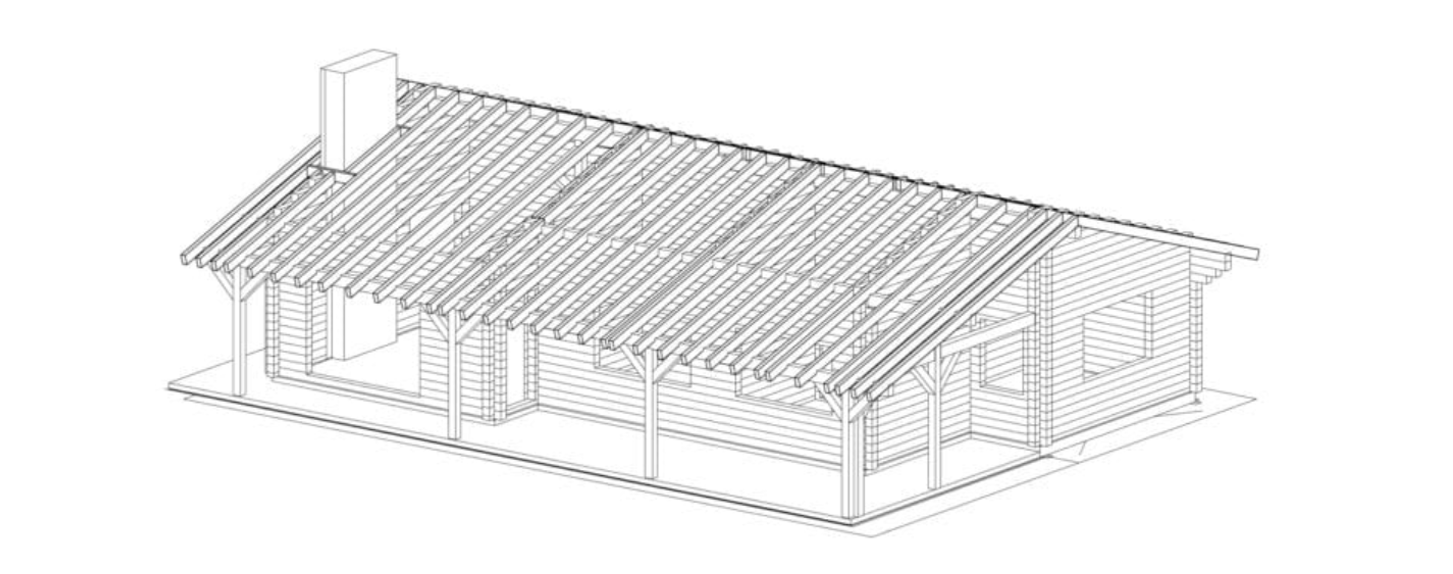
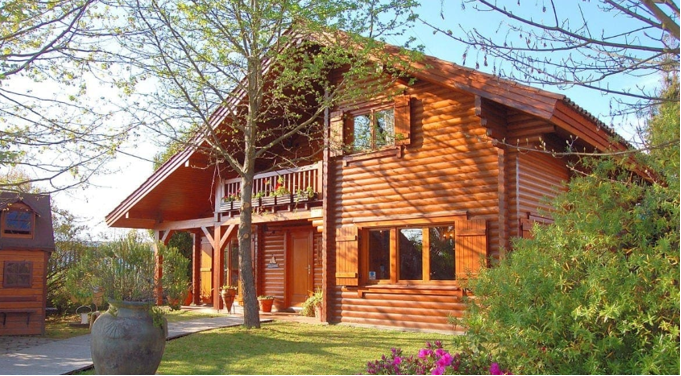
Figure 1: Log houses (Rusticasa, 2022)
Log houses are common in Nordic countries with cold climates and abundant forests, being popular in many regions of Sweden, Finland, Norway, Russia and other areas close to the Baltic Sea. This is primarily due to the abundance of conifers (resinous trees) in those regions, which produce solid structural timber logs that are long and relatively straight, facilitating this type of construction. However, log houses can also be found in hot climates, such as in California, in the United States, where they represent a sign of social distinction. In North America, this type of construction became popular after being imported from Europe by immigrants and colonialists who envisaged a robust and rapid solution for their houses in this construction technique.
The first timber constructions date back to the Stone Age. At this time, they were huts supported by logs driven into the ground, vestiges of which have been found in Poland and Turkey, where they were used to store grain. The transition from simple shelter to permanent construction took place as communities began to settle in villages and towns. Although originally intended for secondary uses with very rudimentary structures, construction with logs evolved, to the extent of producing buildings with several stories, mostly in Northern Europe (Figure 2).
In the dawn of the 20th century, construction with logs was cast aside, largely due to its rusticity and handcrafted components. However, this system is currently experiencing a regeneration due to technological improvements which, while maintaining the principles of the original system, benefits from the advantages of prefabrication.
The first log houses emerged around 1880, democratising access to this type of timber construction. The philosophy of prefabrication was presented at the Universal Exhibition of 1889, held in Paris. At the time, the prefabrication of log houses was considered a technological breakthrough for the construction industry.
In this system, wood performed all the wall’s functions: structural, compartmentation, coating, thermal and acoustic insulation and waterproofing. However, members with a width of less than 110 mm usually implied mixed systems, due to requiring structural and thermal reinforcement. Depending on their shape, log sizes can vary between a width of 110-230 mm for circular sections, or 120-150 mm for rectangular sections, and a length of 3 to 15 m, although logs with a length of more than 5 m are less frequent. When longer lengths are required, the members can be joined together at the top sealed by an intermediary piece (wooden tongue or built-in plate) or with interlocks, normally half-lap joints, ensuring the interlocking between continuous members.
Classically, this system arranges the logs horizontally (Figure 3); nevertheless, there are also singular buildings of this construction category with logs arranged vertically. When placed horizontally, the wood works in the direction perpendicular to its grain. From the static point of view, this use of wood is flawed, because its mechanical properties in the direction perpendicular to the grain are 20 to 30 times lower than those in the log’s longitudinal direction, due to its anisotropic constitution. However, the loads acting on log walls in the construction system are not very high. Nevertheless, it is important to take into account the characteristic fluency phenomena of compression in the direction perpendicular to the grain.
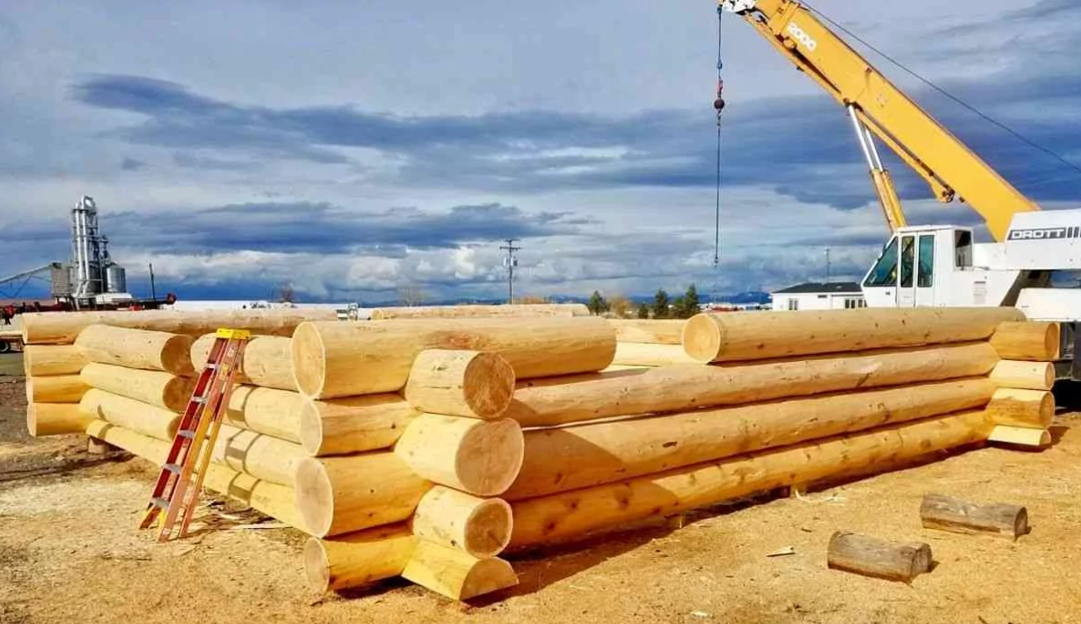
Figure 3: Logs arranged horizontally (Truelog, 2022)
In the past, the logs were previously selected in forests and felled in the winter, when the tree was in a period of minimal vegetative activity (with lower presence of nutrient elements). This process was developed over centuries in order to enhance the durability of the timber members, as the absence of nutrients reduces the risk of attacks by insects and fungi feeding on or living within wood. The log was then stripped and debarked. Drying took place outdoors for one to two years, although in some cases, the construction was started with the drying process being completed on-site. The timber would lose all its remaining water in the summer, and it was hoped that the settling of the logs would be definitive in the autumn. At that time, the joints were sealed with moss and other natural products.
Currently, in industrialised production, the wood is dried in drying chambers, ensuring a water content between 14% and 18%. Water content is an important parameter in this type of construction, as the walls can experience considerable shrinkage cracking as a result of poorly dried logs, with implications in terms of aesthetics, durability and, in some cases, even stability.
Construction stability is ensured by the joinery of the external walls and by the bracing provided by the intermediate walls, which are normally interior (Figure 4).
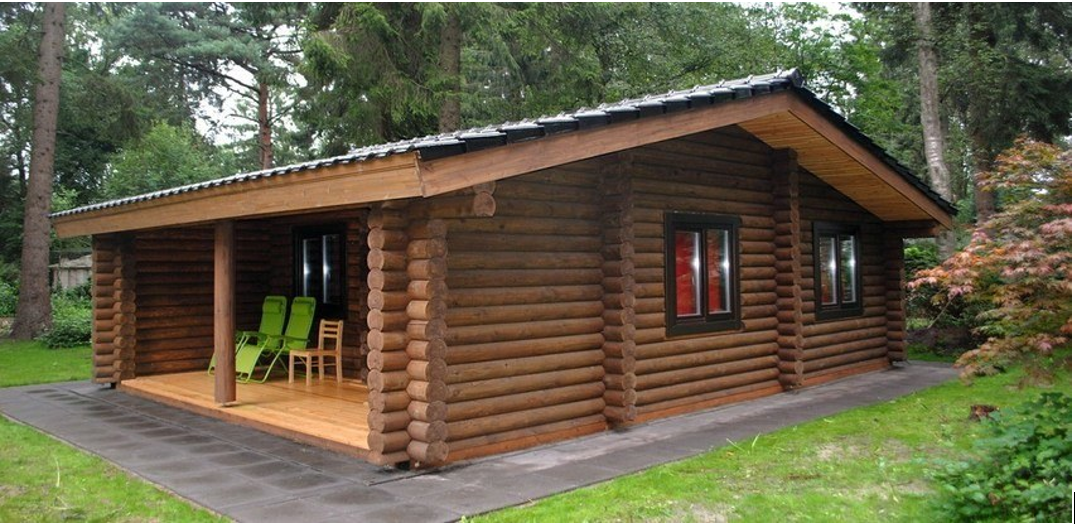
Figure 4: Joinery between the façade walls and intermediary walls
The corner pillars can be done with or without the extension of the parts (Figure 5). The first is more common, using simple fittings or special parts.
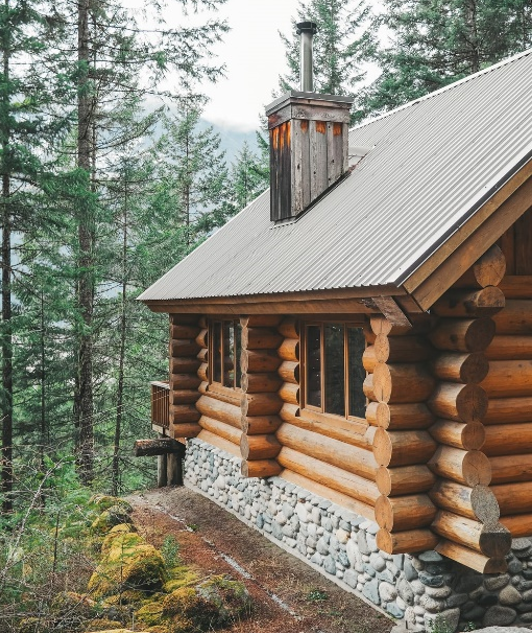
Figure 5: (a) Corner pillars with extension of the parts.
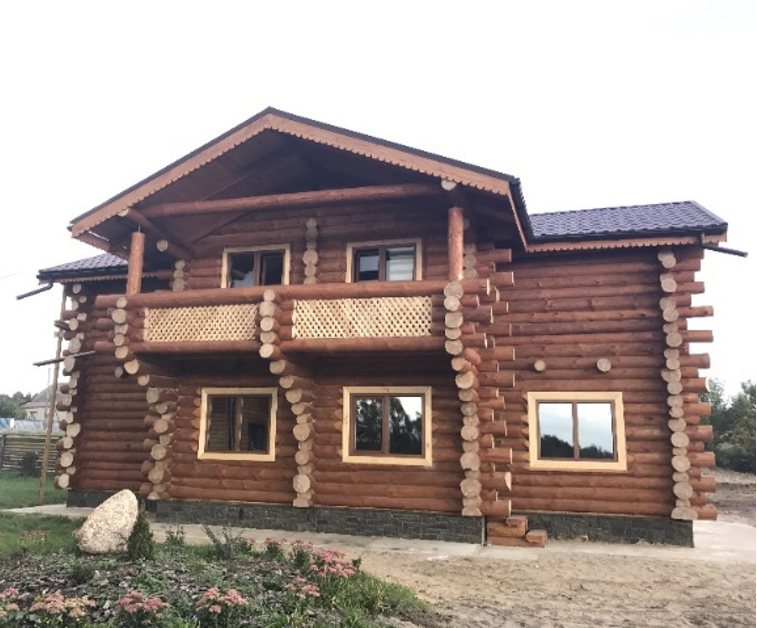
Figure 5: (b) Extension of the parts supporting the balcony structure
The rounded and slightly conical shape of the natural timber logs used in the primitive system made the connection between the walls complex. Therefore, currently, the mechanisation of the process has evolved to use square or rectangular shaped logs which, by providing a greater supporting surface area, contribute to improve stability, facilitate the connection between the members and improve the protection of the joints (Figure 6).
The use of glue laminated timber instead of solid structural timber logs also favours stability against the action of water, due to being a timber product with selected controlled quality features and showing less anisotropy. Nowadays, the wood parts are profiled on 3 or 4 sides and the slots or tongue and groove joints are made at the contact surface. Some models have simple fittings, while others have a clearance space to accommodate the sealing material. In all variations of shapes and fittings, the connection between the members can be completed with dowels and iron fittings. Figure 7 shows some of the main fittings used.
In this construction system, wood is presented in all its expressiveness, entirely reflected in the house’s final appearance, differentiating itself from all the other systems that use wood enveloped in other materials. The log wall is, therefore, an element exposed to rainwater and its members, logs, are responsible for ensuring the building’s waterproofing. Each wood part is treated according to the biological risks and exposure to the climate. Likewise, the connections are designed to prevent the entrance and stagnation of rainwater. In each area of joinery, a sealing strip or barrier ensures impermeability between the parts. Wood, due to its insulation features, prevents reaching dew point, and the existing water vapour inside the building is regulated as a result of the hygroscopic properties of the wood. A log house is naturally insulated, due to the solid structural timber and the large dimensions of the walls; although, supplementary external or internal thermal insulation can be applied, according to the type of climate. From the outside, the logs and sawn wood are usually visible, with the possibility of applying an external transpiring stain. Just as on the exterior, the logs and sawn wood are normally left visible inside, with the possibility of applying a transpiring varnish. Lining or other materials such as plaster, stone, etc. can be applied as finishing, especially if an additional layer of thermal insulation is used (Figure 8).
Before the complete assembly of the parts, it is important to ensure that there are holes for passing through the electrical installation. If there is another wall panel indoors, whether for aesthetic reasons or to accommodate an additional layer of thermal insulation between the wall panels, the electrical installation can be placed inside the chamber formed between the two panels, avoiding interfering in the log structure.
The slabs are usually composed of a system of beams which may, or not, be part of a panel, which rests directly over the log walls. The same happens with the roofing, whose slopes can be formed by supporting the roof members on two log walls or by prefabricated trusses supported by the walls.
Log houses are perfectly adaptable to being assembled in kits; however, this should take into account the dimensional interplay of their walls, especially in the dimensioning of the openings and spans, considering the inevitable vertical settling due to fluency and with a view to minimum waste.