The advantages of construction with wood
The advantages of construction with laminated wood versus concrete and steel
Cross laminated timber (CLT)
Cross laminated timber (CLT) panels are prefabricated, solid and of large dimensions, indicated for structural applications. This is an innovative product, composed of a renewable resource, which permits a high load capacity with low weight, enabling a construction that is lighter but with an extraordinary structural stiffness, and simultaneously preserving the environment and the planet in which we live.
The use of cross laminated timber (CLT) is a valuable resource in civil construction, as it has a mechanical performance similar to that of structures made of concrete, masonry and steel in diverse applications, being a viable solution in the execution of walls, floors and roofs.
Each timber panel, derived from a sustainable forest certified by the Programme for the Endorsement of Forest Certification (PEFC) and Forest Stewardship Council (FSC), is between 6 and 40 cm thick, with its width varying between 120 and 350 cm. Each timber panel, derived from a sustainable forest certified by the Programme for the EndorsAlthough they can be manufactured with sizes tailor-made to each project, the panel dimensions do not usually exceed 13.5 m long and 3 m width due to transport limitations. Large-sized panels fastened together through simple, light and dry connections such as structural adhesive and finger-joints, enable a perfect fit, avoiding the wastage of resin and reducing carbon emissions which are so harmful to the environment. ement of Forest Certification (PEFC) and Forest Stewardship Council (FSC), is between 6 and 40 cm thick, with its width varying between 120 and 350 cm.
A powerful ally in the construction sector, CLT panels can supplement or even substitute conventional structures in numerous design situations, enabling a versatility of uses in construction and can be used combined with any other material.
In wall applications, the timber used in the outer layers of a CLT panel is vertically arranged to enable a higher horizontal load on its fibres, accumulating structural functions, of compartmentation and coating. In flooring and roofs, the timber used in the outer layers of a CLT panel is arranged so that its fibres are parallel to the direction of the span. The high structural rigidity and load capacity of cross laminated timber enable its use in commercial and residential buildings with various stories (the current record is 85 m).
Being provided in the project’s final dimensions and enabling a huge range of finishings pre-installed at the factory, CLT panels have many additional advantages such as thermal protection, acoustic insulation, endurance to side and anti-seismic loads, and resistance to fire.
Being provided in the prThe desire to find a more sustainable profile in civil construction has been driven by the growing demand for alternative, viable, highly durable and high-performance construction products and solutions. CLT panels, arising from technological evolution in the structural use of timber, meet the contemporary requirement of quality and swiftness in construction, energy efficiency and concern for the environment.
Concrete
Concrete is the material most used in civil construction, being composed of a mixture of water, cement and aggregates (broken stone, gravel and sand), which harden the cement paste. In addition to these basic components, concrete can also contain varnish, resin or water-proofing to protect it against the wear and tear of time. Its properties of endurance, adaptability and durability have made the use of this material widespread from ancient times up to modernity. After water, cement is the product most consumed by human beings. Six million tons are produced annually with a myriad of applications, from construction to rehabilitation. Mixed structural members of steel and concrete enable not only reinforcing existing solutions such as pillars and beams, but also building new structures, like mixed beams formed of metal profiles associated with concrete slabs, dimensioned and with a resistance capacity higher than that of the single metal section.
Steel
Steel is an iron and carbon alloy, whose carbon content varies between 0.03% and 2.1%, with cast iron obtained from higher values. The carbon percentage is determinant to define the properties of the different alloys, developed to meet different specifications and conditions, namely high loads, wear and tear, impact, atmospheric corrosion and high temperatures. Steel is the material most used and present in the most varied types of industry, from sewing needle production to oil exploration and extraction not only due to its mechanical properties, but also because of its low cost of production, formation and processing and, due to the abundance of the raw materials comprising it. In civil construction there is a great variety of construction steels, enabling increased resistance in particular parts, strengthening the structure’s resistance to corrosion and durability, with low impact on their volume. In 2021, the world’s steel production amounted to 1.9 billion tons[1], greatly surpassing the production of the most important engineering metal – aluminium.
CLT versus Concrete and Steel
The prefabrication of CLT panels is an industrial process which, despite not being recent, emerged from the companies’ need to squeeze time limits, use more efficient and rational production processes, combined with strict and effective quality control. Its large-sized production and structural rigidity have made it extremely attractive for the civil construction sector, as a supplement to the use of steel and concrete. The issue of environmental conservation is more recent, and has triggered an increasing interest in using CLT as an alternative for “cleaner” construction work, with lower impact of its resources, less wastage, better conditions at the workplace, greater predictability and recyclability.
Initially produced in Austria for the purpose of using less valuable timber, cross laminated timber (CLT) has progressively gained ground worldwide due to its possibilities in terms of quality, durability, reliability and safety of the constructions, not forgetting its minor impact on the environment.
Although the eco-efficiency of cement and concrete is talked about nowadays, the bottom line is that their energy efficiency, durability and recyclability, waste production, energy consumption, carbon dioxide (CO2) emissions and natural resource consumption are still a cause for concern, not only during the construction phase but also later when the buildings are being used.
Cross laminated timber is produced from certified sustainable forest wood, the production of which entails a lower energy consumption than that of concrete or steel, which makes it an excellent measure towards cutting carbon emissions and the use of fossil fuel.
Wood is a natural, renewable and recyclable resource. Wood absorbs CO2 during its growth by fixing carbon for the formation of organic matter, and thus contributing to prevent the greenhouse effect. It should be noted that the CO2 fixed by the tree, by the wood, is only released into the atmosphere when burned. Therefore, felling, processing and recycling operations never release that CO2 into the atmosphere. In other words, wood, and as consequence, timber constructions, operate as batteries storing carbon dioxide storage batteries. The CLT panels are prefabricated, produced in factories, and for this reason generate lower waste on-site compared to other construction materials used in civil construction. It is also possible to reuse parts or segments derived from cutting the panels, such as openings for doors and windows, in different applications or substructures like staircases or other architectural elements.
Initially produced in Austria for the purpose of using less valuable timber, cross laminated timber (CLT) has progressively gained ground worldwide due to its possibilities in terms of quality, durability, reliability and safety of the constructions, not forgetting its minor impact on the environment. Although the eco-efficiency of cement and concrete is talked about nowadays, the bottom line is that their energy efficiency, durability and recyclability, waste production, energy consumption, carbon dioxide (CO2) emissions and natural resource consumption are still a cause for concern, not only during the construction phase but also later when the buildings are being used. Cross laminated timber is produced from certified sustainable forest wood, the production of which entails a lower energy consumption than that of concrete or steel, which makes it an excellent measure towards cutting carbon emissions and the use of fossil fuel. Wood is a natural, renewable and recyclable resource.
As this is the project phase of longest duration, any delays that might occur will be related to lack of knowledge of the product’s potentialities and mechanical properties. There are so many possibilities of use that, as the knowledge level progressively increases during the project phase, there may be a higher number of reviews in design and coordination, which could delay the production phase.
With a resistance comparable to that of concrete, CLT is five times lighter, meaning that when applied to buildings, this helps to reduce the scale of the foundations and the effect of seismic action.
With high durability, excellent thermal, acoustic and electrical insulation, the texture and colour of CLT makes it an aesthetically attractive material.
Regarding regulations, the standard regulating CLT production (EN 16351) [2] was issued in 2014, with a revised version of Eurocode 5 soon to be released that will include this innovative wood derivative. In Portugal, the licensing for this type of house operates in the same way as for a conventional house made of concrete or masonry.
The construction project of a CLT house is associated with different options and phases, from its design, throughout all the work’s planning and execution, up to the phase of its use and operation. Although the project planning phase may require more effort because everything is decided and predetermined in the factory, with all the openings for doors, windows already cut with high precision, the actual construction work and assembly phase are remarkably fast. As this involves industrialised structures, with high structural rigidity, the margin of error (about 2 mm) is very small. It is possible to assemble a 200 m² house in 5 days, just with teams of three to five people. This large-size manufacturing precision gives the builders a high degree of confidence in the product during the construction phase and other suppliers of supplementary materials to confidently prefabricate components required for the construction. As this is the project phase of longest duration, any delays that might occur will be related to lack of knowledge of the product’s potentialities and mechanical properties. There are so many possibilities of use that, as the knowledge level progressively increases during the project phase, there may be a higher number of reviews in design and coordination, which could delay the production phase. With a resistance comparable to that of concrete, CLT is five times lighter, meaning that when applied to buildings, this helps to reduce the scale of the foundations and the effect of seismic action. With high durability, excellent thermal, acoustic and electrical insulation, the texture and colour of CLT makes it an aesthetically attractive material. Regarding regulations, the standard regulating CLT production (EN 16351) [2] was issued in 2014, with a revised version of Eurocode 5 soon to be released that will include this innovative wood derivative. In Portugal, the licensing for this type of house operates in the same way as for a conventional house made of concrete or masonry.
Although there may be a higher cost related to transport and assembly, the construction costs of CLT panels are competitive compared to steel and concrete construction costs. The labour required to erect the structures is lower and the worksite time is substantially lesser. Most of the volume of work is carried out in the factory, in other words, in a controlled environment, for delivery to the implementation site as structures ready for use that merely need to be assembled. This also enables the capacity to accurately estimate the costs of all the project phases before their implementation.
[1] https://worldsteel.org/wp-content/uploads/2021-World-Steel-in-Figures.pdf
[2] https://www.en-standard.eu/csn-en-16351-timber-structures-cross-laminated-timber-requirements-2
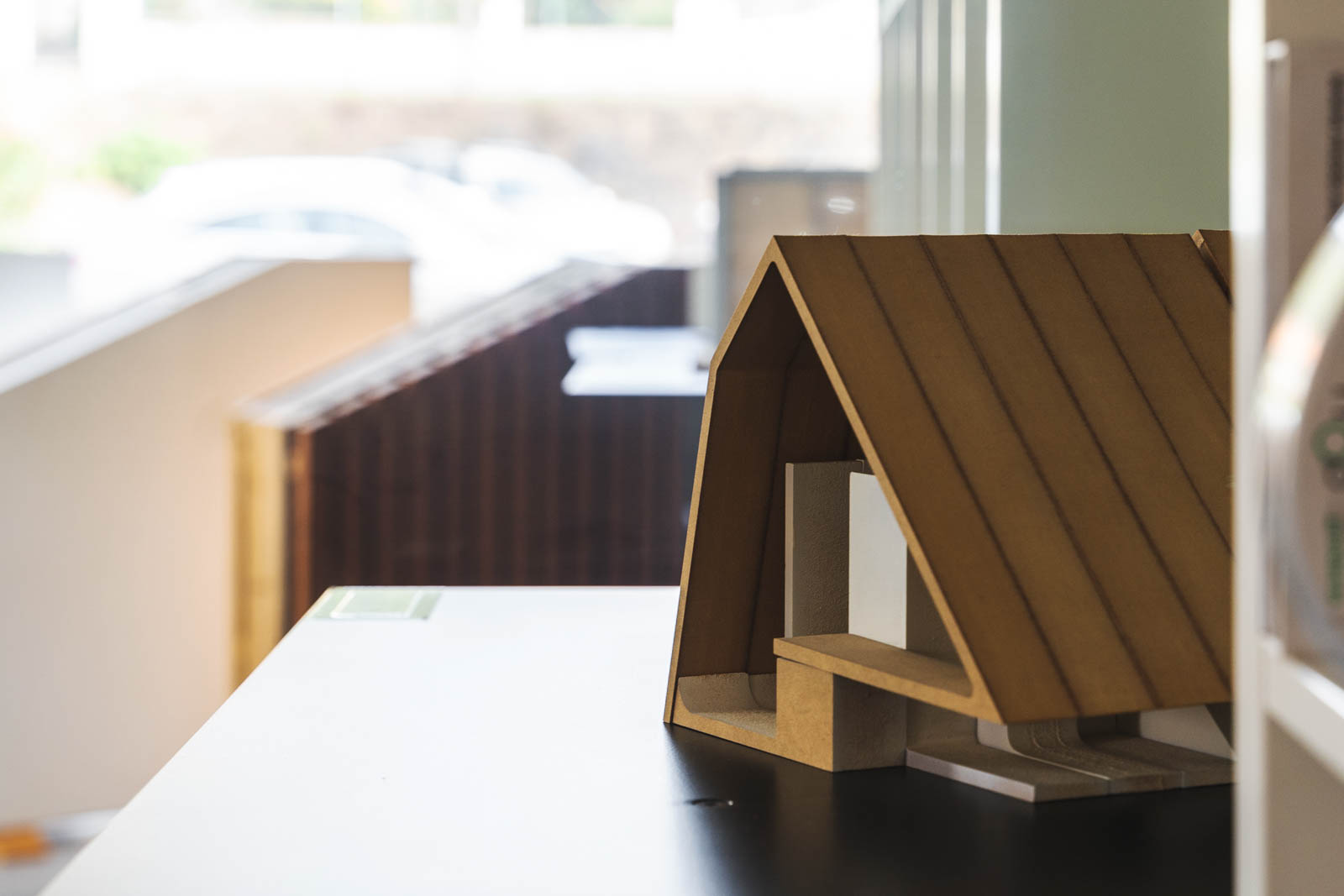
Related Articles
UncategorizedConstruction with Wood
Engineered Wood Market Size & Share Analysis
Government has introduced a statutory tree and woodland cover target which commits to increasing…
Why Choose Wood?Construction with Wood
Timber in construction roadmap
Government has introduced a statutory tree and woodland cover target which commits to increasing…
Durability of construction with wood
The durability of a timber construction can be high. There are examples of wooden churches…